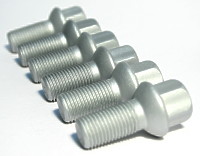
Layer thickness information refers to average values acc. to DIN EN ISO 4042 and DIN EN ISO 10683.
Grade A (2-layer coating)
> 5 – 8 µm
Grade B (3-layer coating)
> 8 – 12 µm
Chromium-VI-free
Pb-free
Cd-free
RoHS-compliant
Corrosion resistance acc. to ISO 9227 NSS:
Depending on layer structure, geometry and application technology, up to 1000h without FeK
Temperature resistance / baking temperature
Up to 250°C / approx. 300°C
Color
Silver
Properties
- High corrosion protection
- No hydrogen embrittlement
- Resistance against UV radiation, fuels, oils, organic solvents, biodiesel, coolant, brake fluid
- Electrical conductivity
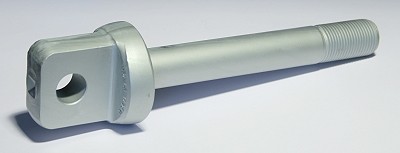
Layer thickness information refers to average values acc. to DIN EN ISO 4042 and DIN EN ISO 10683.
Grade A (2-layer coating)
> 5 – 8 µm
Grade B (3-layer coating)
> 8 – 12 µm
Chromium-VI-free
Pb-free
Cd-free
RoHS-compliant
Corrosion resistance acc. to ISO 9227 NSS:
Depending on layer structure, geometry and application technology, up to 1000h without FeK
Temperature resistance / baking temperature
Up to 250°C / approx. 300°C
Color
Silver
Properties
- High corrosion protection
- No hydrogen embrittlement
- Resistance against UV radiation, fuels, oils, organic solvents, biodiesel, coolant, brake fluid
- Electrical conductivity
- Pre-integrated PTFE lubricant

- Geomet 321® + Plus® ML black
- Geomet 500® + Plus® M black
Layer thickness information refers to average values acc. to DIN EN ISO 4042 and DIN EN ISO 10683.
- Geomet 321/500® (2-layer coating) + Plus® ML, M black (2-layer coating)
- 10 ¨C 15 ¦Ìm
Chromium-VI-free
Pb-free
Cd-free
RoHS-compliant
Corrosion resistance acc. to ISO 9227 NSS:
- > 800h without FeK
- > 240h without ZNK
Temperature resistance / baking temperature
Up to 250°C / approx. 300°C
Color
Black
Properties
- High corrosion protection
- No hydrogen embrittlement
- System coating (Geomet 321® + Plus® ML, M black)
- Resistant against contact corrosion
- Resistant against automotive fluids/li>
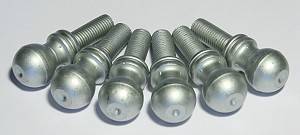
- Plus® VL
- Plus® VLh
- Plus® L
- Plus® ML
- Plus® ML (EU)
- Plus® ML (US)
- Plus® M
- Plus® XL
- Plus® 10
- Plus® ML black
- Plus® M black
Coefficients of friction with threaded parts acc. to test method EN ISO 16047
- Plus® VL > 0.09 ¨C 0.14 ¦Ìtot
- Plus® VLh > 0.09 ¨C 0.14 ¦Ìtot
- Plus® L > 0.08 ¨C 0.14 ¦Ìtot
- Plus® ML > 0.10 ¨C 0.16 ¦Ìtot
- Plus® ML (EU) > 0.10 ¨C 0.16 ¦Ìtot
- Plus® ML (US) > 0.10 ¨C 0.16 ¦Ìtot
- Plus® M > 0.12 ¨C 0.18 ¦Ìtot
- Plus® XL > 0.06 ¨C 0.09 ¦Ìtot
- Plus® 10 > without PTFE, no defined friction coefficient window
- Plus® ML black > 0.10 ¨C 0.16 ¦Ìtot
- Plus® M black > 0.12 ¨C 0.18 ¦Ìtot
(Specified friction coefficient window with reservation!! Exact friction coefficient determined on the respective product).
Chromium-VI-free
Pb-free
Cd-free
RoHS-compliant
Corrosion resistance acc. to ISO 9227 NSS:
- The corrosion protection mechanism of Dacromet® and Geomet® is further improved with a topcoat of PLUS®.
Layer thickness information refers to average values acc. to DIN EN ISO 4042 and DIN EN ISO 10683.
- Plus® VL, VLh, L, ML, M, XL, 10> 1 ¨C 3 ¦Ìm
- Plus® ML, ML (EU), ML (US), M black> 2 ¨C 5 ¦Ìm

Layer thickness information refers to average values acc. to DIN EN ISO 4042 and DIN EN ISO 10683.
Per layer approx. 2 ¨C 4 um
Chromium-VI-free
Pb-free
Cd-free
RoHS-compliant
Corrosion resistance
- Guarantees cathodic corrosion protection as required in DIN EN ISO 10683
- Complies with salt spray test DIN EN ISO 9227 as required in DIN EN 13858
- Complies with salt spray test DIN EN ISO 9227 as required in DIN EN ISO 10683
- Complies with salt spray test DIN EN ISO 9227 as required in DIN EN ISO 2944-6
- Complies with constant climate test acc. to DIN EN ISO 6270-2 (CH)
- Complies with the cyclical corrosion test acc. to VW PV 1200
- Complies with the accelerated corrosion test (ACT Test) acc. to Volvo STD 423-0014
- Complies with the accelerated corrosion test (ACT II Test) acc. to VCS 1027,1449
- Delays contact corrosion
Media resistance
- Complies with chemical resistance requirements against operating materials acc. to DIN EN ISO 2812
Temperature resistance
- Maintains corrosion protection after medium thermal stress (up to 400¡ãC) over a longer period of time.
Temperature resistance
- Maintains corrosion protection after medium thermal stress (up to 400¡ãC) over a longer period of time.
Color
Properties
- Inorganic
- Solvent-based
- Increased protection against red and white corrosion
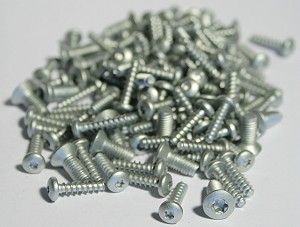
Layer thickness information refers to average values acc. to DIN EN ISO 4042 and DIN EN ISO 10683.
Per layer approx. 2-4 um
Chromium-VI-free
Pb-free
Cd-free
RoHS-compliant
Corrosion resistance acc. to ISO 9227 NSS:
- Depending on layer structure, geometry and application technology, up to 1000h without FeK
Temperature resistance / baking temperature
- Up to 180¡ãC / approx. 200¡ãC
Color
Properties
- High corrosion protection
- No hydrogen embrittlement
- Electrical conductivity

- Delta® Seal silver
- Delta® Seal silver GZ
- Delta® Seal black
- Delta® Seal black GZ
- Delta® green and other variants on request
Coefficients of friction with threaded parts acc. to test method EN ISO 16047
- Delta® Seal silver> without lubricant additive, no defined friction coefficient window
- Delta® Seal silver GZ> 0.09-0.14 utot
- Delta® Seal black > without lubricant additive, no defined friction coefficient window
- Delta® Seal black GZ> 0.09-0.14 utot
(Specified friction coefficient window with reservation!! Exact friction coefficient determined on the respective product).
Chromium-VI-free
Pb-free
Cd-free
RoHS-compliant
Corrosion resistance acc. to ISO 9227 NSS:
- The corrosion protection mechanism of Delta® Protekt and Delta® Tone is further improved with a topcoat of Delta® Seal.
Layer thickness information refers to average values acc. to DIN EN ISO 4042 and DIN EN ISO 10683.
- Per layer approx. 2-4 um
- Multiple layers possible
- With black surfaces, a 2-layer coating (topcoat) is needed at a minimum

Together with oiling, phosphating serves as a temporary protection against corrosion
- Delta Protekt® – VH 300
- Delta Protekt® – VH 301 GZ
- Delta Protekt® – VH 302 GZ
- Delta Protekt® – VH 321 GZ (black)
Coefficients of friction with threaded parts acc. to test method EN ISO 16047
- Delta Protekt® - VH 300> without lubricant additive, no defined friction coefficient window
- Delta Protekt® - VH 301 GZ> 0.09 - 0.14 utot
- Delta Protekt® - VH 302 GZ> 0.10 - 0.18 utot
- Delta Protekt® - VH 321 GZ (black)> 0.08 - 0.16 utot
(Specified friction coefficient window with reservation!! Exact friction coefficient determined on the respective product).
Chromium-VI-free
Pb-free
Cd-free
RoHS-compliant
Corrosion resistance acc. to ISO 9227 NSS:
- The corrosion protection mechanism of Delta® Protekt and Delta® Tone is further improved with a topcoat of Delta Protekt® - VH …
Layer thickness information refers to average values acc. to DIN EN ISO 4042 and DIN EN ISO 10683.
- Per layer approx. 2-4 um
- Multiple layers possible
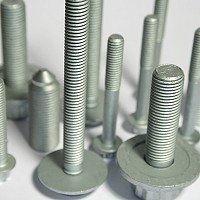
Magni Flake B46
Layer thickness information refers to average values acc. to DIN EN ISO 4042 and DIN EN ISO 10683.
- Per layer approx. 2 - 4 um
Chromium-VI-free
Pb-free
Cd-free
RoHS-compliant
Corrosion resistance acc. to ISO 9227 NSS:
- Depending on layer structure, geometry and application technology, up to 1000h without FeK
Temperature resistance / baking temperature
- Up to 180°C / approx. 200°C
Color
Properties
- Coating compatible with aluminum
- No hydrogen embrittlement
- Electrical conductivity
- Resistant against: acidic/alkaline/organic fluids, e.g., antifreeze, brake fluid and fuels

- Magni Top B18 (Magni 565)
- Magni Top B28N
- Magni Top E10A
- Coefficients of friction with threaded parts acc. to test method EN ISO 16047
Coefficients of friction with threaded parts acc. to test method EN ISO 16047
- Delta® Seal silver> without lubricant additive, no defined friction coefficient window
- Delta® Seal silver GZ> 0.09-0.14 utot
- Delta® Seal black > without lubricant additive, no defined friction coefficient window
- Delta® Seal black GZ> 0.09-0.14 utot
Coefficients of friction adjustable according to requirements
Chromium-VI-free
Pb-free
Cd-free
RoHS-compliant
Corrosion resistance acc. to ISO 9227 NSS:
- The corrosion protection mechanism of Magni Flake B46 is further improved with a topcoat of Magni Top ¡
Layer thickness information refers to average values acc. to DIN EN ISO 4042 and DIN EN ISO 10683.
- Per layer approx. 2-4 um
- Multiple layers possible