Grade 8 fasteners are manufactured of medium carbon alloy steel for the most demanding applications. These fasteners are then quenched and tempered to superior strength and hardness qualities.
The grade marking on a Grade 8 fastener is six equally-spaced lines coming out from the center of the head. The manufacturer mark is necessary for traceability.
Stainless Steel
Stainless steels achieve “stainless” characteristics by virtue of their ability to form a tight adherent film of iron-chromium oxide which strongly resists attack by the atmosphere and a wide variety of industrial gases and chemicals. This effect, plus the superior high temperature strength characteristics exhibited by many of these alloys, accounts for their wide use at ordinary and elevated temperatures with a wide choice of mechanical properties and several distinct levels of corrosion resistance.
These steels may be subdivided into the following four groups:
Martensitic stainless steels are iron-chromium alloys which are hardenable by heat treatment. Representative of this group are Types 410, 420, 431 and 440C.
Ferritic stainless steels are iron-chromium alloys which cannot be hardened significantly by heat treatment. Representative of this group are Types 405 and 430.
Austenitic stainless steels are iron-chromium-nickel and ironchromium-manganese-nickel alloys which are hardenable by cold working. Representative of this group are Types 201, 304, and 316.
Precipitation hardening stainless steels are iron-chromium-nickel alloys with additional elements which are hardenable by solution treating and aging.
Alloys in the first two groups are magnetic in all conditions; those in the third group are slightly magnetic in the cold worked condition, but non-magnetic in the annealed condition in which they are most often used. Alloys in the fourth group are magnetic in the precipitation hardened condition.
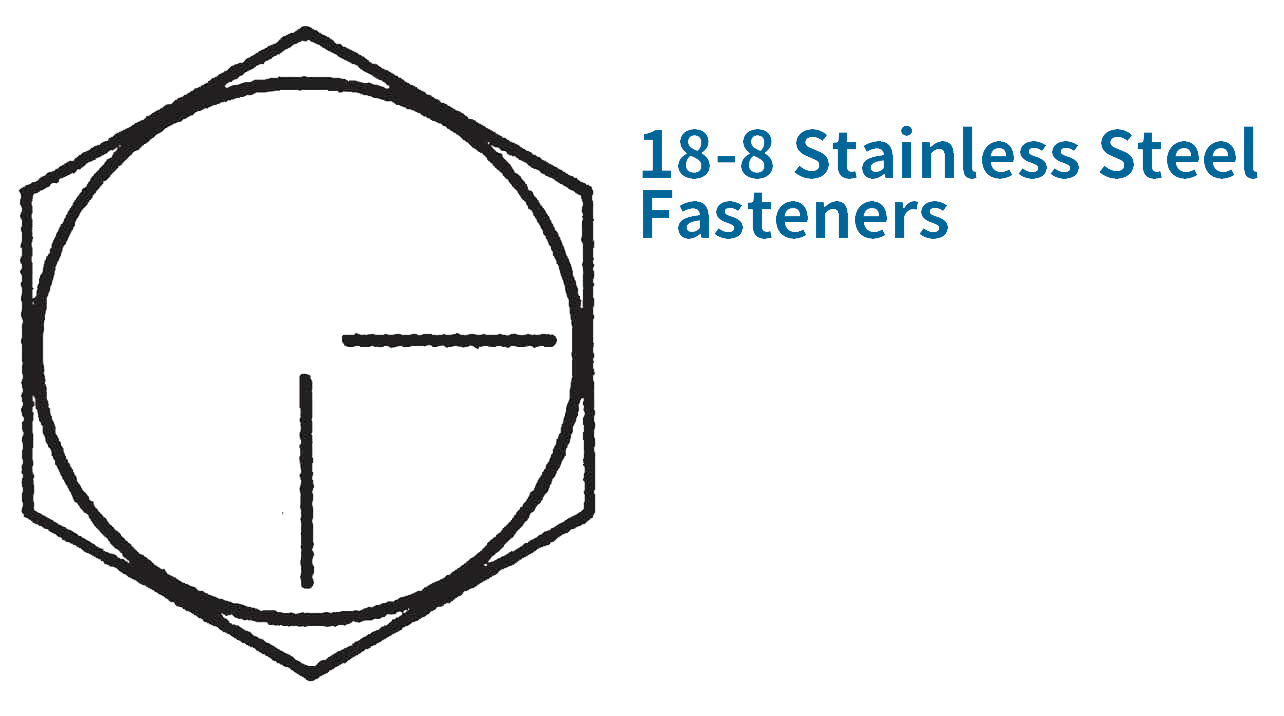
18-8 Stainless Steel
This is the most popular type of stainless used in the production of fasteners. Its composition is approximately 18% chromium and 8% nickel, thus the name 18-8. Several grades of stainless are included in this classification including 302, 303, 304 and 305. These all have good strength and corrosion resistance.

316 Stainless Steel
This is more corrosion resistant than 18-8, but also more expensive. It is composed of approximately 18% chromium and 12% nickel with the addition of 2% to 4% molybdenum. It also maintains its strength at higher temperatures than 18-8.
410 Stainless Steel
It has approximately 12% chromium with no nickel. It is not very corrosion resistant and is magnetic, but it can be heat treated to become harder.
Exotic Metals
Alloy 20
This alloy has approximately 20% chromium and 34% nickel plus 3% to 4% molybdenum. It is very corrosion resistant and is especially popular when in contact with sulfuric acid.
Brass
This metal is approximately 65% copper and 35% zinc. It offers a good combination of strength, corrosion resistance and workability.
Nickel Copper 400
This alloy is approximately 70% nickel and 30% copper. It has excellent strength and corrosion resistance and is used in salt water marine and other chemical environments.
Titanium
This has a very high strength to weight ratio, as well as good corrosion resistance.
Inconel
Registered trademark of Inco Ltd.
Composed of approximately 77% nickel and 15% chromium. It offers superior strength and good corrosion at high temperatures.
Silicon Bronze
It is composed of approximately 96% copper, 3% silicon and 1% manganese. It is more corrosion resistant and tougher than brass. It is widely used in the electrical industry.